Are you tired of dealing with constant basement flooding? Look no further than the Zoeller M53 sump pump, a reliable and efficient solution to keep your basement dry. However, even the best of pumps can encounter problems over time. If you’re facing issues with your Zoeller M53 sump pump, don’t worry! In this guide, we will walk you through how to troubleshoot common problems and restore your pump to its optimal performance.
With its powerful motor and durable construction, the Zoeller M53 sump pump has become a popular choice for homeowners looking to prevent water damage. However, like any mechanical device, it can encounter issues such as excessive noise, failure to turn on, or inadequate pumping capacity. These problems can be frustrating and disruptive, but fear not! By following a few simple troubleshooting steps, you can diagnose and resolve most common problems with your Zoeller M53 sump pump, saving you time and money in the process. So, let’s dive in and get your sump pump back in action!
Table of Contents
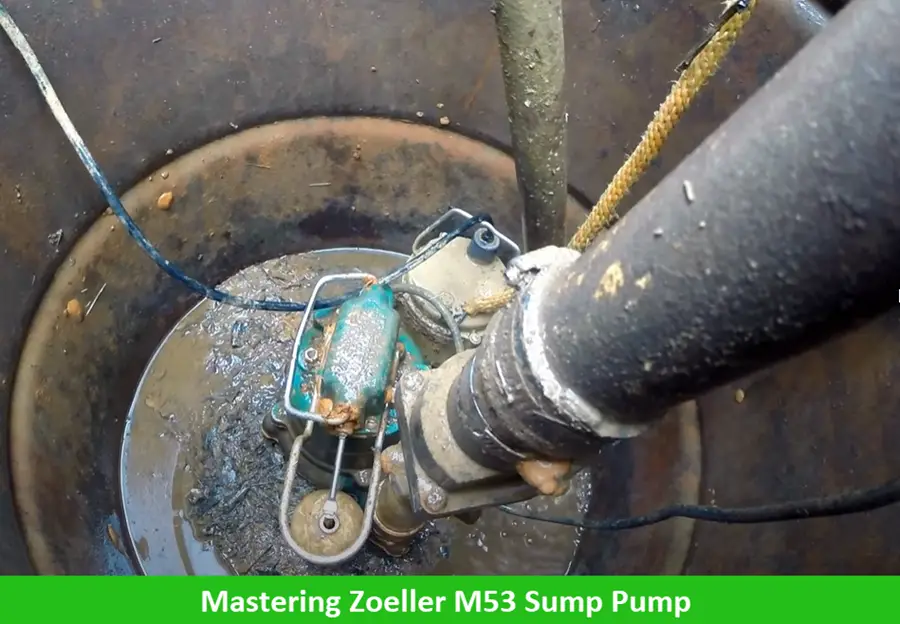
How to Troubleshoot Zoeller M53 Sump Pump Problems:
- Check the power supply to ensure the pump is receiving electricity.
- Inspect the float switch to make sure it moves freely and is not stuck.
- Clean the pump and remove any debris that may be causing clogs.
- Inspect the discharge pipe for any blockages or leaks.
- If the pump is running but not removing water, check the impeller for any damage or obstruction.
How to Troubleshoot Zoeller M53 Sump Pump Problems
Welcome to this step-by-step guide on troubleshooting Zoeller M53 sump pump problems. In this article, we will walk you through common issues that may arise with your Zoeller M53 sump pump and provide you with practical solutions to resolve them. By following these instructions, you’ll be able to troubleshoot and fix most problems, ensuring the efficient functioning of your sump pump.
1. Pump Not Turning On
If your Zoeller M53 sump pump is not turning on, there are a few potential causes to consider.
First, check the power supply. Ensure that the pump is properly plugged in and that the circuit breaker or fuse is not tripped or blown.
If the power supply is not the issue, move on to inspecting the float switch.
Make sure the float switch is freely moving and not obstructed by debris. Clean the float switch if necessary.
- Residential 3 year warranty
- 3/10 hp, 9.6 Amps, 115 Volts
- Cord Length 9 Feet, Gauge 18/3
- Residential Application; 1-1/2″ NPT Discharge
If the power supply and float switch are both functioning correctly, the problem may lie with the pump itself. Check the pump’s motor for any signs of damage or overheating. If the motor appears damaged or is excessively hot, it may need to be repaired or replaced. Additionally, inspect the pump’s impeller for any clogs or blockages. Remove any debris that may be hindering the impeller’s rotation. If none of these steps resolve the issue, it’s recommended to contact a professional for further assistance.
2. Pump Running Continuously
If your Zoeller M53 sump pump runs continuously, it can be a sign of a problem that needs attention. Start by examining the float switch. Ensure that the float switch is not stuck in the “up” position, as this can cause the pump to continuously run. If the float switch appears to be functioning correctly, check the discharge pipe for any leaks or blockages. A leak or obstruction in the discharge pipe can create a continuous flow of water, triggering the pump to run non-stop.
Another possible cause of continuous pump operation is a malfunctioning check valve. The check valve prevents water from flowing back into the sump pit after the pump has turned off. If the check valve is faulty, water can freely flow back, causing the pump to activate repeatedly. Inspect the check valve for any signs of damage or obstruction and replace it if necessary. Finally, make sure that the sump pit is not excessively filled with water. If the water level is too high, it can trigger the pump to run constantly. Adjust the float switch or install a higher float switch if needed.
3. Unusual Noises
If your Zoeller M53 sump pump is making unusual noises, it’s essential to identify the source of the noise to determine the underlying problem. Start by checking for any loose or damaged parts. Tighten any loose bolts or screws and replace any damaged components. Unusual noises can also be caused by a clogged or obstructed impeller. Inspect the impeller for any debris and clean it thoroughly. If the noise persists, it may be an indication of a motor issue. Contact a professional for further evaluation and repair.
By following these troubleshooting steps, you can address common problems that may arise with your Zoeller M53 sump pump. Remember to always prioritize safety and consult a professional if you are unsure or unable to resolve the issue yourself. Regular maintenance and inspection of your sump pump can help prevent problems from occurring and ensure its optimal performance.
Should I Buy A Better Version Of The Zoeller M53?
The Zoeller M57 is a better quality sump pump in that it has all cast iron parts instead of the plastic parts on the M53 model
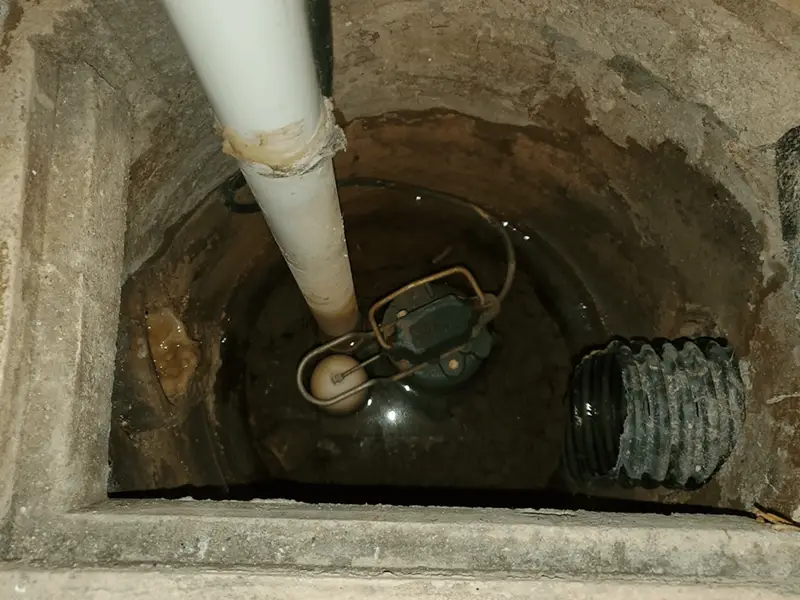
Zoeller M53 submersible sump pump in a sump basin.
Frequently Asked Questions
Here are some commonly asked questions about troubleshooting Zoeller M53 sump pump problems.
1. How do I check if my Zoeller M53 sump pump is receiving power?
To check if your Zoeller M53 sump pump is receiving power, start by ensuring that it is properly plugged into a working electrical outlet. Check the circuit breaker or fuse box to make sure the circuit is not tripped or the fuse is not blown. If the power source and circuit are working correctly, inspect the power cord for any damages or loose connections. Additionally, you can use a multimeter to test the power supply at the pump’s electrical terminals. If no power is detected, it may indicate a faulty power cord or pump motor that needs further inspection or repair.
If the pump is receiving power but still not functioning, it may be due to other issues such as a stuck or clogged impeller, a faulty float switch, or a malfunctioning switch. These components should be inspected and tested to identify the root cause of the problem and take appropriate corrective measures.
2. Why is my Zoeller M53 sump pump not pumping water out?
If your Zoeller M53 sump pump is not pumping water out, there could be a few potential causes. Firstly, check the discharge pipe or hose for any obstructions or clogs that may be preventing the water from flowing out. Clear any debris or blockages if found. Secondly, verify that the pump’s impeller is not jammed or obstructed. You can do this by disconnecting the pump from the power source and manually rotating the impeller to check for any resistance or blockage. If there is an obstruction, remove it carefully to restore proper functionality.
Additionally, ensure that the float switch is not stuck in the “off” position, as this can prevent the pump from activating. Clean the switch and ensure it moves freely. If the pump still does not pump out water, it may indicate a malfunctioning motor or other electrical issues that require professional inspection and repair.
3. Why is my Zoeller M53 sump pump running continuously?
A Zoeller M53 sump pump running continuously can be caused by a few different factors. First, check the float switch to ensure it is not stuck in the “on” position. If it is stuck or obstructed, clean it and test its movement. A faulty or misaligned float switch may need to be replaced to resolve the issue.
Another possible cause is a high water level in the sump pit, indicating a problem with the pump’s capacity to keep up with the water flow. In this case, you may need to consider installing a larger capacity pump or addressing any drainage issues that are causing excessive water buildup. It’s also important to check for any leaks or cracks in the discharge pipe or hose, as these can contribute to continuous running by allowing water to recirculate back into the sump pit.
4. How do I prevent my Zoeller M53 sump pump from overheating?
To prevent your Zoeller M53 sump pump from overheating, make sure it is properly sized for the intended application. Running a pump that is too small for the required workload can cause it to overheat.
Regular maintenance is also crucial in preventing overheating. Clean the pump and remove any accumulated debris or dirt that can restrict its operation. Inspect the impeller and motor for any signs of wear or damage. Lastly, regular testing and inspection of the pump’s components can help identify any issues before they escalate and cause overheating.
5. How often should I test and maintain my Zoeller M53 sump pump?
It is recommended to test and maintain your Zoeller M53 sump pump at least once a year, preferably before the rainy season or when heavy precipitation is expected. Regular testing ensures that the pump is functioning correctly and can handle the water flow. To test the pump, pour water into the sump pit until the float switch activates the pump. Observe the pump’s operation, including the activation, pumping out water, and shutting off. If any abnormalities are noticed, further inspection or maintenance may be required.
In terms of maintenance, clean the pump and sump pit, removing any debris or dirt that can affect the pump’s performance. Check the power cord and electrical connections for any damages or loose connections. Inspect the impeller and motor for signs of wear or damage. Lubricate the pump’s bearings as recommended by the manufacturer. Regular maintenance helps prolong the lifespan of the pump and ensures its reliable operation when needed.
In conclusion, troubleshooting Zoeller M53 sump pump problems doesn’t have to be a daunting task. By following the steps outlined in this guide, you can identify and address common issues that may arise with your sump pump. Remember to start with the basics, such as checking for power supply and ensuring proper installation, before moving on to more complex problems.
By being proactive and regularly maintaining your sump pump, you can prevent potential issues and ensure that it continues to function effectively when you need it the most. So, don’t let sump pump problems cause unnecessary stress. Take charge and troubleshoot with confidence, knowing that you have the knowledge and tools to keep your basement dry and protected. In conclusion, troubleshooting Zoeller M53 sump pump problems is a crucial skill that every homeowner should have.
- Residential 3 year warranty
- 3/10 hp, 9.6 Amps, 115 Volts
- Cord Length 9 Feet, Gauge 18/3
- Residential Application; 1-1/2″ NPT Discharge
Float arm sticks and pump won’t turn on when float is at max hieght! All things clear and clean
I assume that you meant the metal arm sticks. That would mean that the switch is not working. Replace the Cap and Switch Assembly
https://amzn.to/4bCLM19 /]